Boost Your LED Production
Flex Neon Lights Silicone Extrusion Machine Factory
The silicone extrusion machine is specifically designed for the efficient manufacturing of waterproof silicone LED flexible light strips. By automatically encasing the LED strip within a protective layer of silicone, this production line offers enhanced durability and longevity for your lighting products. Our versatile machine can accommodate various silicone strip types, making it the go-to solution for all your LED strip production needs. Upgrade your LED manufacturing process with our state-of-the-art Flex Silicone Neon Lights Extrusion Machine.
Get A Quote Ask for Specification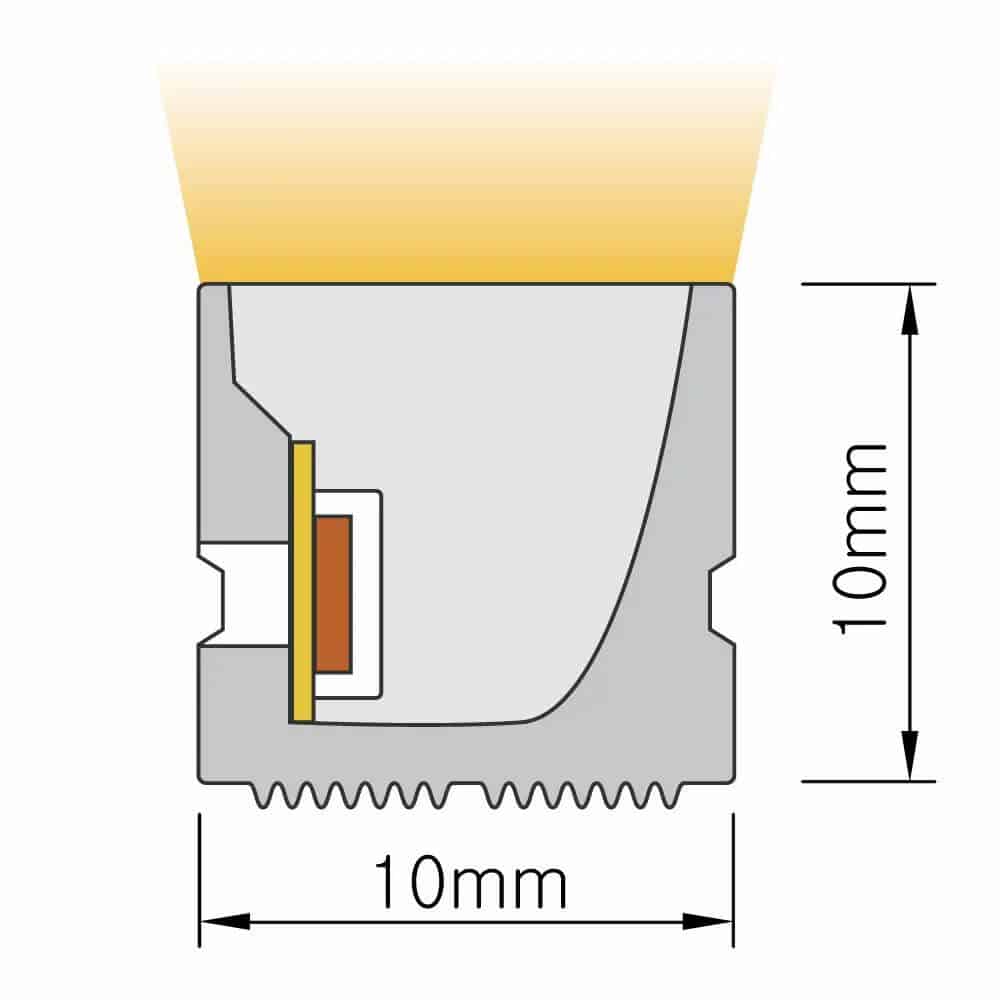
Solid core strip lights
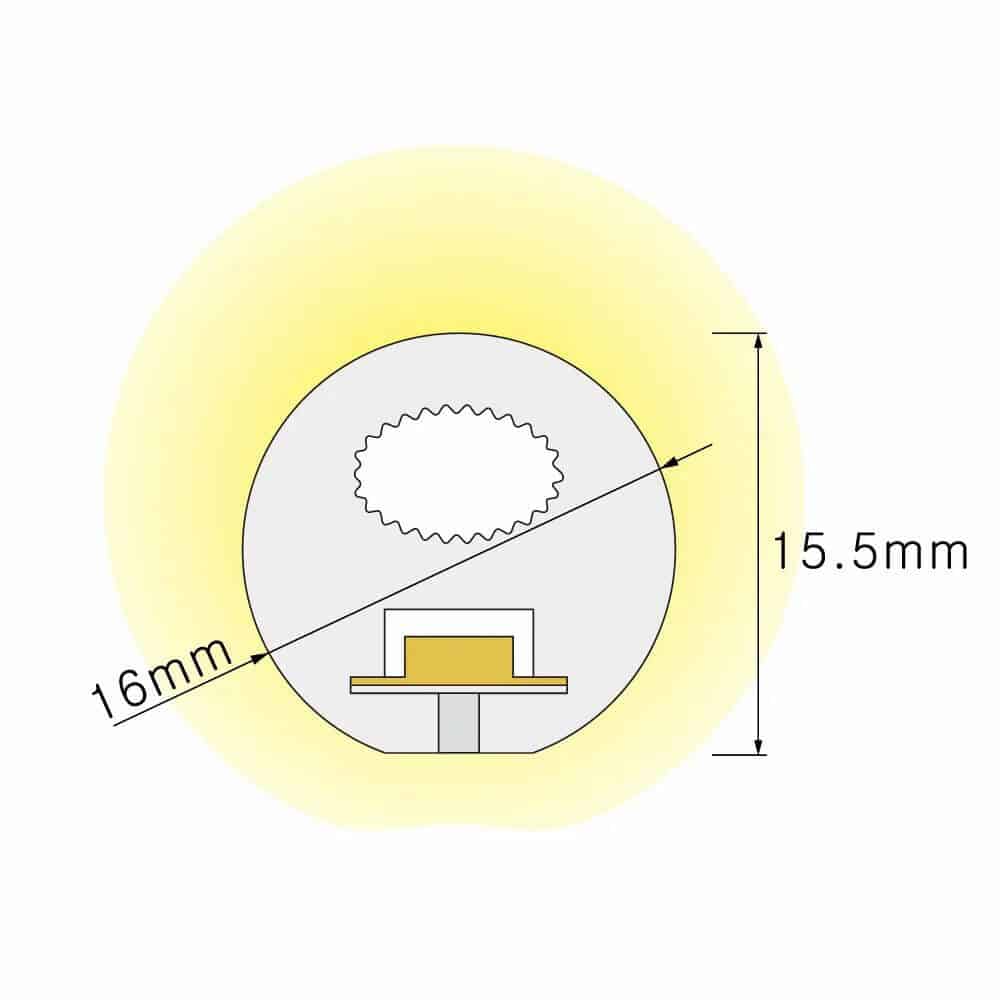
Tubular strip lights
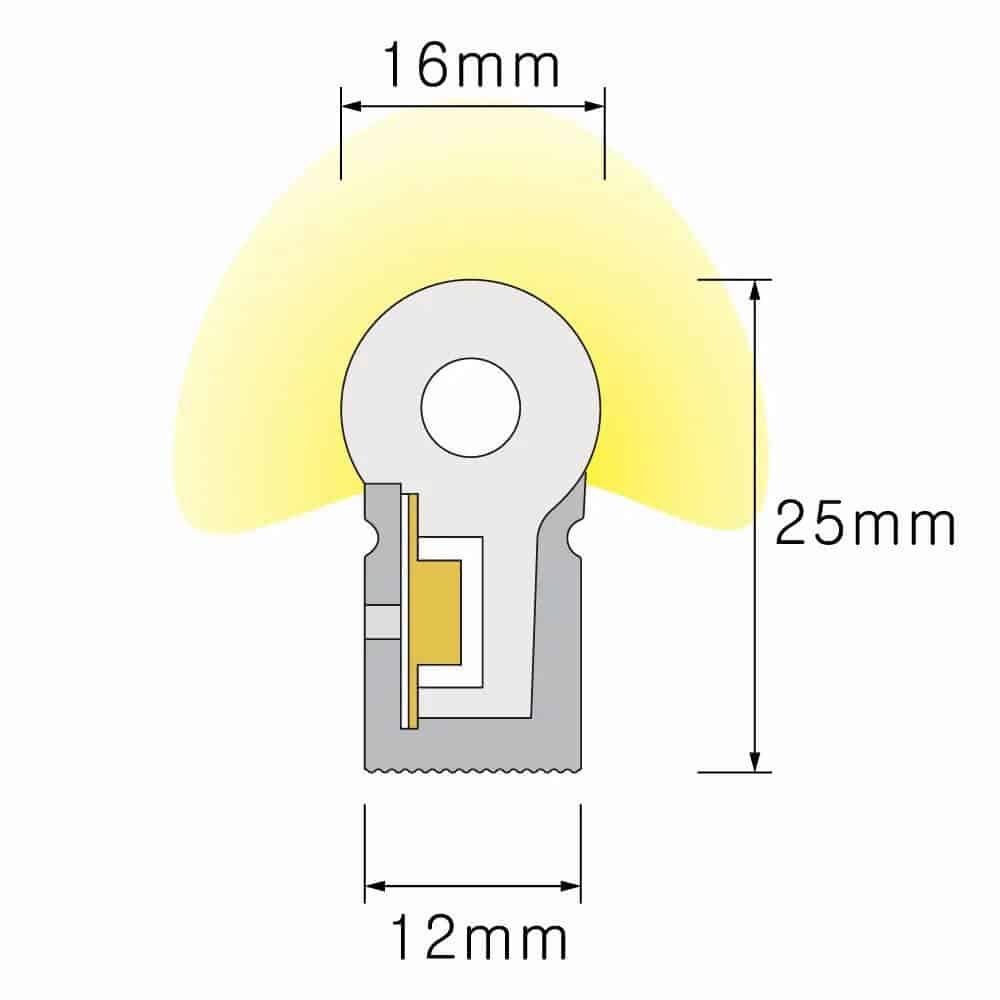
Semi-tubular strip lights
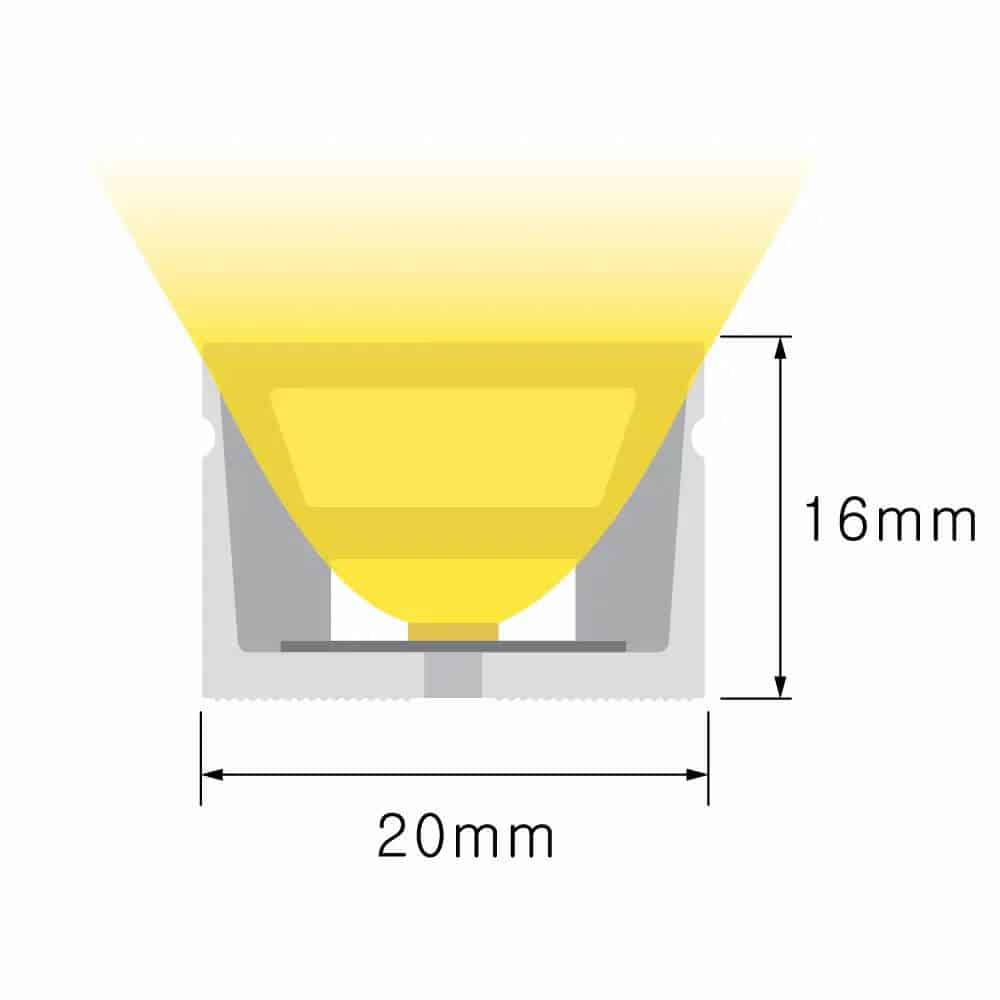
Bi-color neon strip lights