Epoxy glue, with its unique properties, serves as a game-changer in various fields. Understanding the ins and outs of this versatile adhesive – including its properties, uses, and benefits – is essential for professionals and DIY enthusiasts alike. This comprehensive guide will also introduce an innovative tool that significantly enhances the application process of epoxy glue – an automatic dispensing machine.
Understanding 2 Part Epoxy Glue
What Exactly is a 2 Part Epoxy Glue?
A 2 part epoxy glue is a formidable adhesive system that comprises two distinct components: a resin (Part A) and a hardener (Part B). These components are chemically inactive when stored separately, maintaining their liquid forms. However, upon mixing, they initiate an exothermic chemical reaction that results in the creation of a potent adhesive bond. This bond boasts robust resistance to heat, chemicals, and mechanical stress.
This powerful adhesive system exhibits a broad adhesion spectrum, making it a versatile solution for various materials. These materials include but are not limited to, wood, metal, glass, ceramic, and certain plastics. The varying grades of 2-part epoxy glue cater to diverse tensile strength requirements, thermal resistances, and flexibility needs, rendering it a highly customizable adhesive option.
The Inner Workings of 2 Part Epoxy
The potency of the 2-part epoxy glue lies in the chemical process known as “cross-linking.” Upon mixing the resin and the hardener, a chemical reaction gets underway. This reaction fosters the creation of a polymeric chain of interconnected molecules. As the mixture begins to cure, these chains proliferate and interweave, forming a rigid, durable plastic-like material.
This curing process, which can be fine-tuned by manipulating factors such as temperature, humidity, and the ratio of resin to hardener, is what transforms the liquid epoxy mixture into a solid. This transformation imparts the 2-part epoxy with its characteristic strength and durability. The resultant bond is not only robust but also displays resistance to creep deformation under long-term load, making it suitable for heavy-duty applications.
Further, the cross-linked structure of the cured epoxy also gives it superior resistance to chemical and environmental degradation, making it suitable for use in harsh or demanding conditions.
Drying and Curing Process
Drying Time of 2 Part Epoxy Glue
Following the application of 2-part epoxy glue, a key element in achieving an effective bond is allowing the adhesive sufficient time to dry. This drying phase, also known as the “open time” or “working time,” depends on various factors. These include ambient temperature, relative humidity, the thickness of the adhesive layer, and the specific chemical formulation of the epoxy system in use.
Typically, the epoxy may dry to the touch within minutes to several hours. However, this doesn’t necessarily indicate complete drying. It’s imperative to ensure that the epoxy has entirely dried before progressing with your project. Premature handling may disturb the bonding process, potentially compromising the integrity and strength of the adhesive bond.
Curing of 2 Part Epoxy Resin
Curing represents the final, decisive step in the application process of 2-part epoxy resin. Unlike drying, which involves the evaporation of solvents, curing is a chemical process that further hardens the epoxy. This step significantly enhances the epoxy’s physical properties, including its durability, thermal stability, and resistance to environmental factors.
The curing process, also known as the “set time,” can take considerably longer than drying, with the duration ranging from several hours to days. This time frame depends largely on the specific epoxy formulation and environmental conditions such as temperature and humidity.
Moreover, post-curing, a process where the bonded assembly is subjected to elevated temperatures for an extended period, can further enhance the mechanical and thermal properties of the epoxy.
During the curing process, the epoxy achieves its maximum strength and becomes fully resistant to a range of factors, including moisture, heat, and various chemicals. Thus, understanding and respecting the curing time is critical to ensuring the maximum performance of the 2-part epoxy resin in your project.
Characteristics and Benefits of 2 Part Epoxy Glue
1. Durable Bonding: Strength and Hardness
One of the defining characteristics of 2-part epoxy glue is its incredible strength. Once the two components are mixed and cured, the resulting bond is exceptionally durable and hard. This high strength allows epoxy to withstand significant mechanical stress, making it ideal for heavy-duty applications in industries like construction, automotive, and aerospace.
2. Versatile Adherence: Bonding a Wide Range of Materials
2-part epoxy glue is incredibly versatile. It can effectively bond a variety of materials, including wood, metal, glass, ceramics, and many plastics. This versatility makes it a favorite among DIY enthusiasts and professionals alike, as it can be used in numerous projects ranging from home repairs to complex industrial assemblies.
3. Temperature and Chemical Resistance
Epoxy glue is highly resistant to temperature fluctuations and various chemicals, including acids, alkalis, and solvents. This resistance makes it suitable for environments exposed to harsh conditions or extreme temperatures, such as engine parts, industrial machinery, and outdoor structures.
4. Superior Water Resistance
A fully cured 2-part epoxy forms a waterproof seal, resistant to prolonged exposure to moisture and water. This property enables epoxy glue to be used effectively in applications that require water-resistant bonding, such as plumbing repairs, boat construction, and outdoor furniture assembly.
5. Extended Shelf Life
When stored separately and properly, the resin and hardener have a long shelf life. This means you can keep unused epoxy for future projects without worrying about it losing its effectiveness over time.
6. Comparison Between 2 Part Epoxy, Urethane and Silicone
Property | 2 Part Epoxy | Urethane | Silicone |
---|---|---|---|
Curing Time | Moderate (minutes to hours) | Fast (minutes to hours) | Slow (hours to days) |
Adhesion Strength | High | Moderate | Low |
Temperature Resistance | High | Moderate | High |
Chemical Resistance | High | Moderate to High | Moderate |
Flexibility | Low to Moderate | High | High |
Water Resistance | High | Moderate to High | High |
Ease of Use | Moderate (requires accurate mixing) | Easy | Easy |
Cost | Moderate to High | Moderate | Moderate to High |
Suitable Applications | Metal bonding, plastic repairs, high-stress applications, automotive repairs, marine repairs, flooring and construction applications | Flexible molds, clear coatings, prototypes, electrical potting and encapsulation | Sealing, bonding, gaskets, high temperature applications, electrical insulation, waterproofing |
Applications of 2-Part Epoxy: Versatility with Precision
2-part epoxy’s versatility is one of its primary strengths. This powerful adhesive has been found beneficial in an array of applications, thanks to its ability to create a strong bond between a wide variety of materials. From everyday DIY projects to specialized industrial uses, 2-part epoxy has made a significant impact.
Automotive and Aerospace Industries
In the automotive and aerospace industries, 2-part epoxy is commonly used in the assembly and repair of parts. It aids in bonding body panels, fixing cracks, and even filling small holes in metallic components. The epoxy’s high-temperature resistance makes it suitable for parts exposed to heat.
Construction and Home Improvement
In construction and home improvement, 2-part epoxy is often used for concrete repairs, including filling cracks in floors and walls. Its waterproof properties also make it ideal for applications that require water resistance, such as plumbing repairs and sealing around sinks or bathtubs.
Electronics
In electronics, 2-part epoxy is employed to encapsulate or pot electronic assemblies. This process provides the assemblies with mechanical strength, prevents the ingress of moisture, and protects them from shock and vibration.
Crafts and Hobby Activities
Crafting enthusiasts often turn to 2-part epoxy for projects that need a clear, durable finish. From jewelry making to woodworking, this adhesive is known for its strength and high-quality finish.
The Role of Automatic Dispensing Machines in Epoxy Application
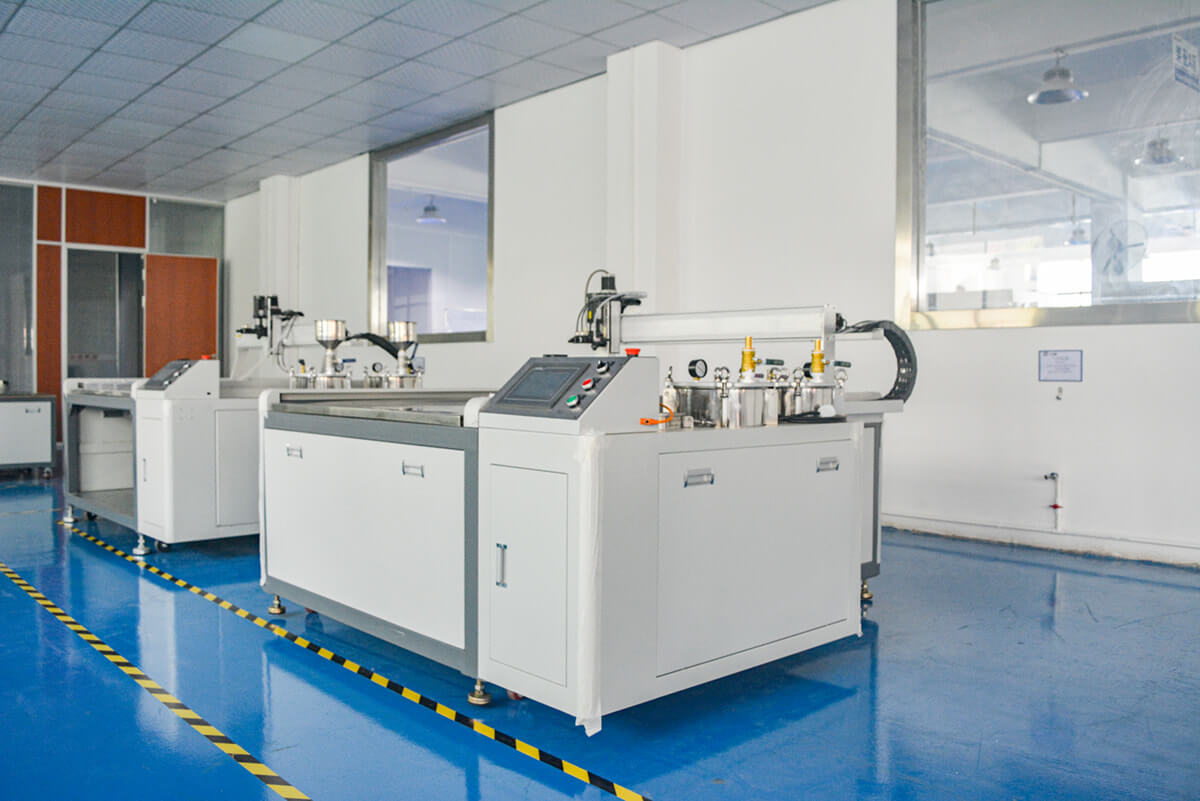
While manual application can be sufficient for small, DIY projects, precision and consistency become critical in industrial applications or when working on a larger scale. This is where our automatic dispensing machine becomes an invaluable tool.
The machine is not just an asset for delivering the exact quantity of the 2-part epoxy but also for ensuring an accurate mix. Incorrect proportions can lead to an ineffective bond or a finish that doesn’t meet standards, but our machine eliminates that risk.
Furthermore, for applications such as electronic assembly potting, where epoxy needs to be dispensed into small, intricate areas, the precision of an automatic dispensing machine is unparalleled. It guarantees the efficient, clean, and precise application of the adhesive, even in complex geometries. This level of precision, combined with the machine’s consistency and speed, can significantly increase productivity and reduce material waste in the long run.
Preparing and Applying 2 Part Epoxy Glue with Your Automatic Dispensing Machine
Mixing 2 Part Epoxy: Precision at its Best
The automatic dispensing machine simplifies and enhances the process of mixing 2-part epoxy. By precisely metering and mixing the resin and hardener, it ensures a perfect blend that maximizes the epoxy’s adhesive properties. With this machine, you no longer need to worry about inaccurate proportions or uneven mixing – it handles the meticulous process, allowing you to focus on the application.
Applying the Epoxy: Smooth and Consistent
Applying 2-part epoxy can be a messy and challenging task, especially for large-scale or complex projects. However, with the automatic dispensing machine, application becomes a seamless operation. The machine dispenses the epoxy evenly and accurately, ensuring optimal coverage and bond strength. Its design also prioritizes safety, with features to minimize the risk of spills and accidents during application.
Conclusion
In the realm of adhesives, 2-part epoxy glue holds a unique position due to its unrivaled bonding strength, versatility, and water-resistant properties. However, to truly tap into these benefits, precise preparation and application are crucial – a task made seamless by the automatic dispensing machine. By accurately mixing and applying the epoxy, this machine lets you focus on what matters most: creating exceptional, durable projects with the power of epoxy glue. Whether you’re a professional contractor or a DIY enthusiast, integrating an automatic dispensing machine into your tool arsenal can significantly enhance your epoxy application process, leading to superior results.